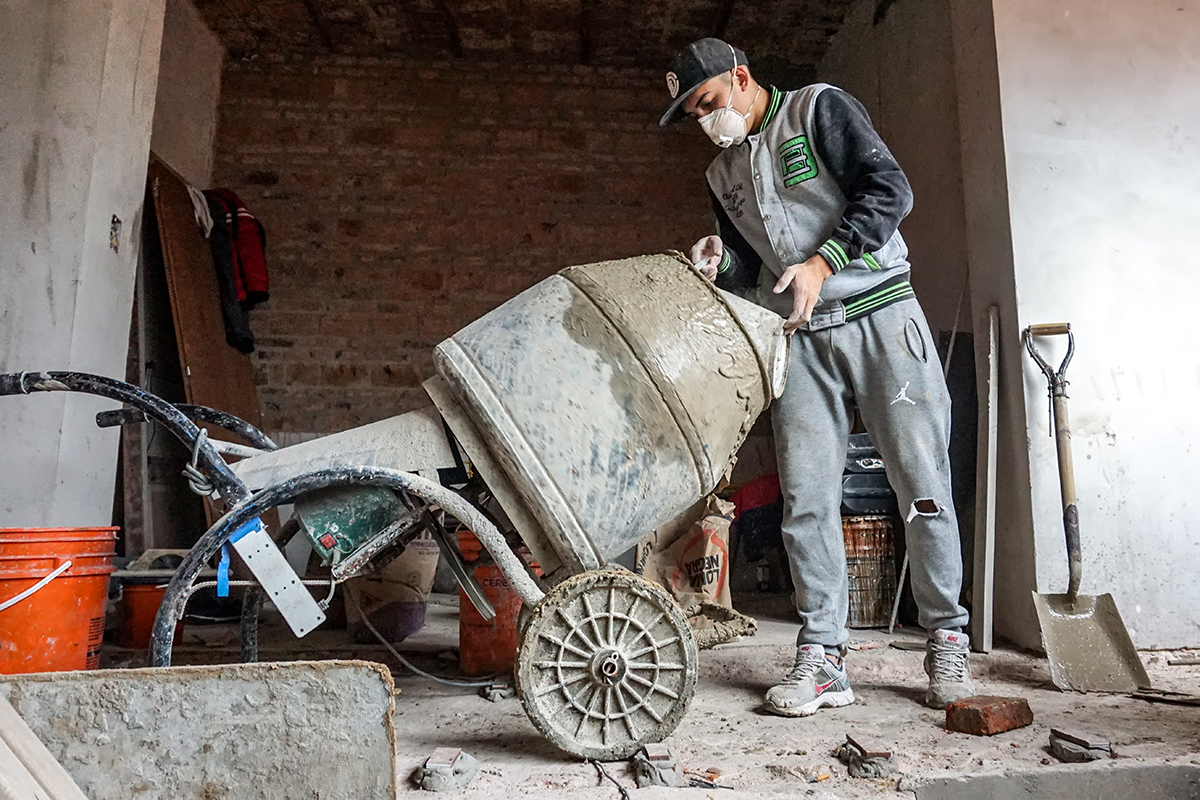
Lucila Pellettieri, GPJ Argentina
Carlos Legal mixes cement for a subfloor in a home in Buenos Aires, Argentina. Legal worries that his government’s interest in prefabricated housing kits from China will put him out of work.
BUENOS AIRES, ARGENTINA — In 2017, Noelia Martínez secured a government loan of 300,000 Argentine pesos (about $7,600 in today’s dollars) to buy her first home. At the time, the home she hoped to buy would have cost about 770,000 pesos (about $19,500 today).
But when Martínez saw the value of the Argentine peso drop from 20 pesos to the dollar to a fraction of just one over just a few months earlier this summer, her hopes were dashed. The government loan she qualified for was no longer enough to buy the home she needed, which was by then priced at more than 1 million pesos (now about $25,380). The value of the peso continues to drop. As of late-September, the exchange rate was around 39 pesos per dollar.
Martínez says she’d already sold her car to make the down payment. She hopes she can cancel the loan.
“It would be a shame to give up the dream of our own house, but there are not many alternatives,” she says.
Martínez lives with her husband and two children in the back of her mother-in-law’s house.
Her predicament is common in Argentina, where official sources estimate that 25 percent of all households suffer from a housing deficit, meaning that their homes are too small for their families.


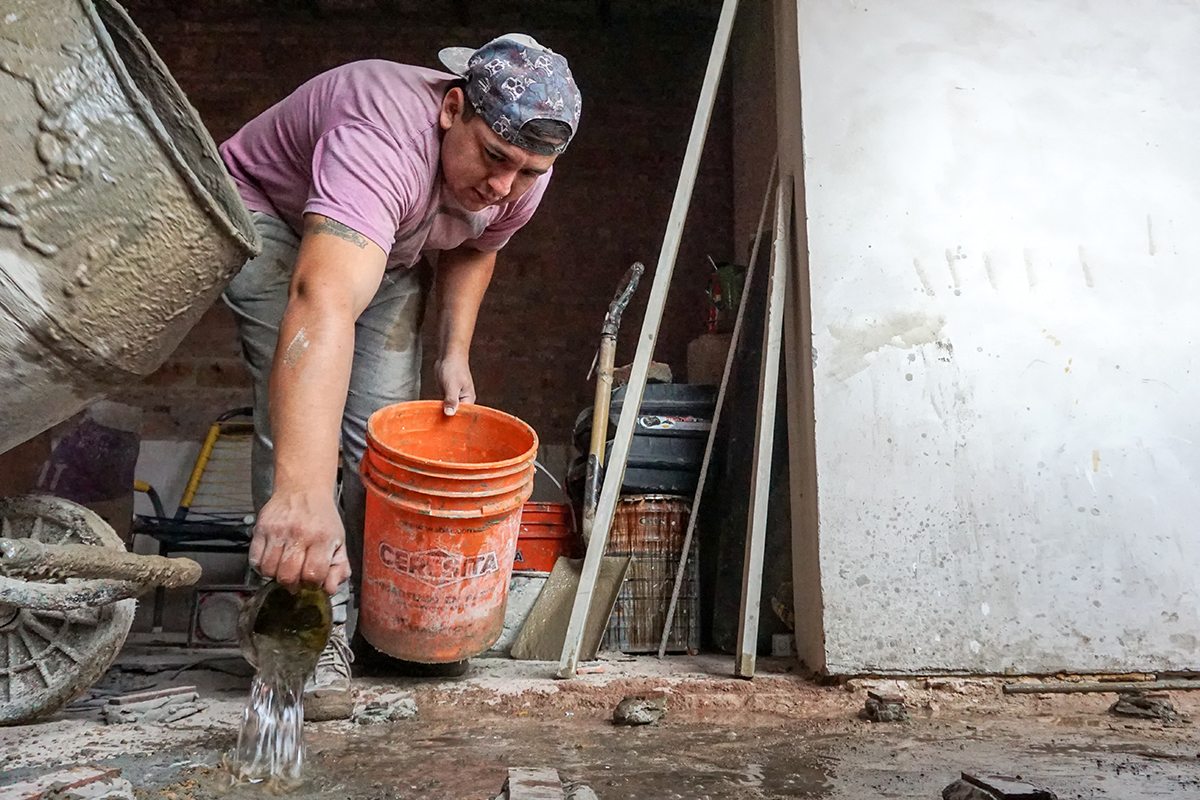
The housing crisis was sparked by Argentina’s roller-coaster economy. A 2001 economic free fall reduced salaries and limited job options for Argentina’s middle class, ultimately displacing many to the informal job market. Meanwhile, housing prices shot way up, and the availability of affordable housing didn’t keep pace with growing demand.
But officials at the nation’s housing ministry say they have a possible solution: prefabricated home kits, manufactured quickly and cheaply, then built on-site in Argentina, at a price fully covered by a ProCreAr loan – the same loan that Martínez received. However, the manufacturers would likely be foreign companies.
The government’s ProCreAr loans are doled out via a lottery system, with a preference for single-parent families, applicants with children, people with disabilities and other vulnerable groups.
This year, the government is expected to send out a call for proposals to companies that manufacture those kits in Argentina, says Marcelo Busellini, the national design director at the housing ministry. Government officials expect that most of the companies that bid on the work will be Chinese-owned, he says.
It is the first time that Argentina has carried out an international bidding process for housing construction, Busellini says.
The objective is to build 10,200 homes on public land by mid-2019. That’s just a tiny percentage of the 1.5 million homes needed, according to data provided by the government’s urban development and housing department. If the first phase goes smoothly, the project could spread rapidly, with many thousands of homes built quickly, Busellini says.
Recipients of the first homes built will be those who have already qualified for ProCreAr loans – people like Martínez.
“We want to reduce the housing deficit without indebting the country,” Busellini says.
But there’s a hitch: Once the housing kits are provided by a company, likely a foreign one, that same company will also be contracted to assemble them, Busellini says. Seven or eight workers will be able to construct a single home in a week, he says.
That could all but destroy the nation’s construction industry, local builders say.
The government expects that the total cost to build a single home will be about $800 (31,500 pesos) per square meter. By comparison, the median home value in the U.S. is $1,615 (63,600 pesos) per square meter.
It’s a price that Federico Carreto, a board member for the province’s construction federation, believes the local industry can match.
“We are not far from those numbers. The cost of building a middle, upper-middle class house is $1,100 (43,300 pesos) per square meter. If social or large quantity housing is being built, those values have to go down,” Carreto says.
His main concern is that the new construction model, which the government says could turn around the housing crisis, could also leave many people unable to work on what may wind up being the largest building project in the nation.
That’s a natural consequence of industrialization, Carreto says.
“No matter how much work is done by the national workforce, there will be few people running high tech machines,” Carreto says.


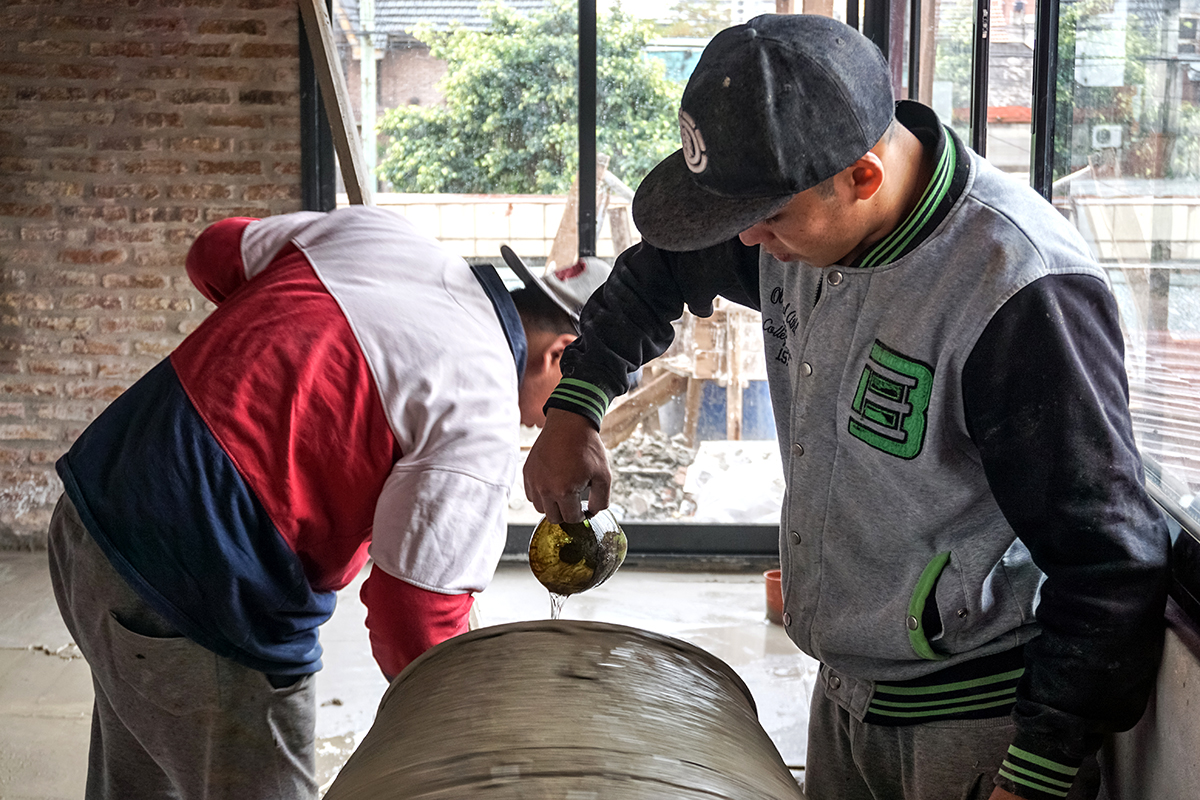
Prefabricated structures are a growing trend globally, especially in areas with housing shortages. In the U.S., work involving prefabricated components grew from 13 percent of all construction in 2010 to 35 percent in 2016, according to research published by the Fails Management Institute, a construction and engineering consulting firm.
In late 2016, a U.K. housing association announced a partnership worth 2.5 billion British pounds ($3.2 billion dollars) with the China National Building Material Company to build six factories in the U.K., which are expected to produce 25,000 prefabricated home kits each year. Local and global news sources report that China Wu Yi is launching a precast building-materials factory in Kenya. The factory will produce building components, including prefabricated steel structures.
This isn’t a new concept. In the early 1900s, Sears, Roebuck and Company sold home kits through its catalog to buyers in the U.S. Some of those homes are still in use, admired for their design.
In Argentina, the construction sector is still growing. It’s the country’s fifth-largest industry, based on the number of registered workers. In June 2018, there were 201,756 workers in private-sector construction, according to a report from the Ministerio de Trabajo, Empleo y Seguridad Social, the labor, employment and social security ministry. The construction industry also relies heavily on informal labor, which isn’t reflected in this report.
The project could also jeopardize the future of Argentina’s brick-makers, since the prefabricated homes are made with wood, steel framing and concrete panels. Right now, brick is used in most construction projects, including large buildings.
“Everything that is imported destroys jobs. This is going to have an important impact on our activity and on many activities within construction,” says Luis Cáceres, secretary general of the national brick-makers’ union. “Bricks are not exported. We depend on internal consumption.”
Brick production is a traditional activity in Argentina. Although there are factories and brick cooperatives, the majority of workers in the sector produce bricks in family kilns, located next to their homes or ranches, Cáceres says.
In 2014, according to government data, there were 160,000 brick-making families in Argentina.
Busellini argues that local companies can’t work at the scale needed to build so many homes at once. Some of the Chinese companies require a minimum of 5,000 homes for a single project, he says.
“There are no local companies that can possibly obtain the financing, nor produce so much volume,” Busellini says.
Carreto admits that Argentine construction firms likely can’t access financing as cheaply as Chinese companies. Interest rates are high for everyone in Argentina because of the country’s economic problems. Carreto even acknowledges that the Chinese firms might be more technologically adept.
“It is pretty unfair competition to compete with companies that have technology, Chinese machines and soft financing that we still don’t have access to,” he says.
Martínez, the mother who was priced out of the housing market due to inflation, says her housing requirements include affordability – meaning she would pay in pesos, not in any foreign currency, no matter how stable.
Her other concerns have little to do with who builds her home. They’re about whether the home will be located in a place where she can build her life.
The proposal to build with housing kits made by foreign companies is “interesting,” she says, but she’s withholding judgment until she’s certain her children can easily access a school, and she can easily access a job.